As part of Ascension Automation Solutions, I had the opportunity to work on a project for ATS Industrial Automation, commissioning error-proofing inspection systems for GM’s battery lines. This was a significant and rewarding experience.
It all started at the ATS campus in Cambridge, Ontario. I was introduced as a contractor from the company I work for, Ascension Automation Solutions. Ascension provides technical labor resources to other automation companies to integrate their equipment. Additionally, Ascension Automation Solutions has its own manufacturing and integration products and services. Located in Cambridge, Ontario, Canada, the company designs, builds, tests, and delivers automation equipment to various customers.
Getting Started
My journey began at the ATS Industrial Automation campus, where I custom-built and developed the camera system for the Factory Acceptance Test (FAT) before deployment. This initial phase was crucial for ensuring the system’s performance and reliability. The cameras were Matrox Cameras, using Design Assistant software, a powerful flowchart-like tool to program inspection systems based on widely available algorithms in the machine vision space.
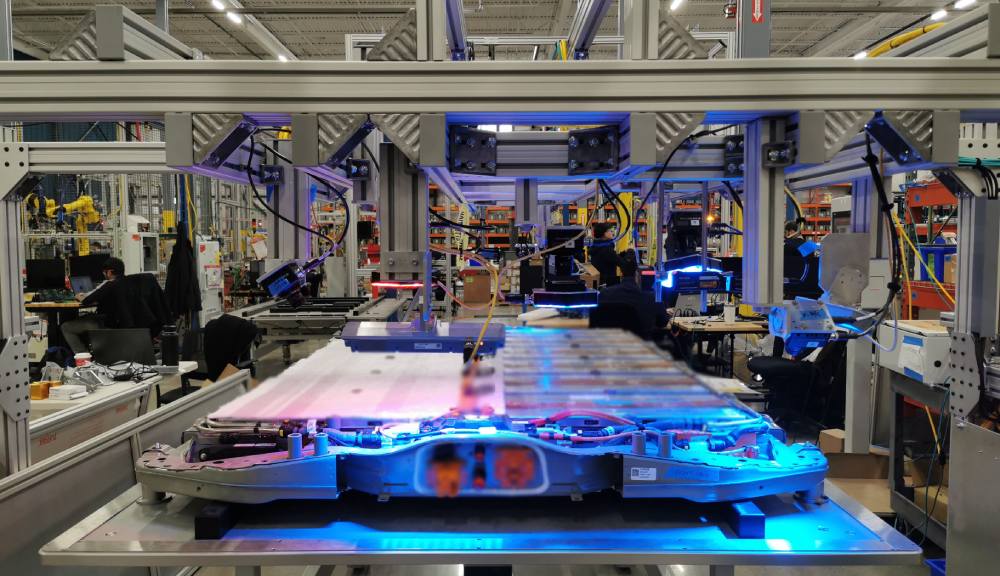
Supervising Installation
Once on-site, At Ramos Arizpe, Mexico, I oversaw the installation of the hardware, ensuring each component was correctly placed and securely mounted. Following that, I undertook the verification of the delivered parts against the ATS design specifications. Although this step was tedious, it was essential to ensure everything was in order.
Hardware Setup
Next, I directed the experimental setup of the cameras and lighting, adjusting angles, focus, and exposure to achieve optimal performance on the battery samples. Using dummy samples provided by GM, we optimized the camera inspection programs, camera direction, and lighting to ensure accurate pass/fail inspections. I also programmed the web interface of the Matrox cameras to allow fine-tuning of inspection parameters on the fly, adapting the program to the variability of samples under test.
Troubleshooting
I encountered and resolved various issues, including cameras restarting randomly due to power problems, cameras not saving inspection images on the camera computer, and unreliable inspections with program updates. Additionally, I gained practical PLC and HMI skills by integrating, testing, and validating various equipment such as stack lights, barcode readers, and torque controllers in manual stations.
Project Management
Aligning our actions with the plant’s deadlines required effective project management. I prioritized my work based on the project’s phases, including N1, N5, N30, PPAP, and production. By coordinating with various teams, I ensured we met our timelines without compromising quality.
During the N1 and N5 phases, I focused on initial setup and verification, ensuring that all systems were correctly installed and operational. In the N30 phase, I concentrated on refining the setup, addressing any issues that arose, and preparing the systems for pre-production validation.
For the PPAP (Production Part Approval Process) phase, I meticulously tested the systems to ensure they met GM’s stringent quality standards. This phase was critical for gaining approval to move into full production.
Once in production, I optimized the inspection systems to achieve full automation with minimal intervention. This involved fine-tuning the cameras and software to ensure reliable, consistent performance, resulting in a 100% automated system.
Collaboration
Working closely with the teams from Ascension, ATS, MTQ4, and GM, we fostered effective communication and teamwork to drive the project to success.
Reflection
Successfully commissioning these systems was a milestone in my career, reinforcing my passion for automation and robotics. This project highlighted the transformative power of technology in the manufacturing space.
Taking the inspection system to a 100% reliable system was an eye-opening journey for me. I strived for full automation, driven by data and a continuous improvement mindset. It required a listening ear and an eager heart, and I am proud of what I achieved on this journey.
Tools and Technologies Employed
- Windows Networking
- Matrox Design Assistant
- Keyence IX-Navigator
- Studio 5000 (Allen Bradley PLC)
- Siemens TIA Portal
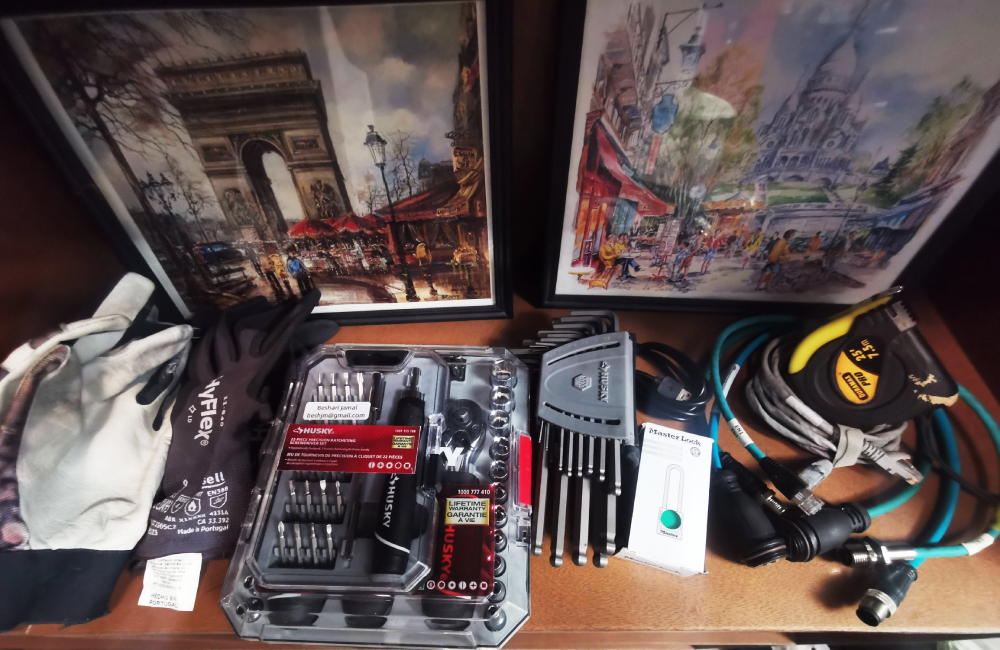
Conclusion
In the end, I am incredibly proud of the fully automated inspection system we developed and deployed. It stands as a testament to the power of collaboration, precision engineering, and the relentless pursuit of excellence. This achievement not only enhances manufacturing quality but also paves the way for future innovations in automation.